Производство золокерамического кирпича должно быть обеспечено непрерывной подачей однородного глинистого материала и фельзита, лишенного каменистых включений имеющего разрушенную природную «структуру» для лучшего смачивания, сохраняющего достаточно постоянную влажность независимо от времени года и равномерно перемешенного с добавками. На керамических заводах сырьевые материалы подвергают грубому, среднему и мелкому дроблению грубому и тонкому помолу. Обычно тонким помолом завершается механическое измельчение материалов, что обеспечивает более интенсивное их спекание, содействует снижению температуры обжига. Измельчение глинистых материалов проводят последовательно на вальцах грубого и тонкого измельчения. Каменистые включения не могут быть полностью выделены из глины общепринятыми механическими приемами – дезинтеграторными ребристыми вальцами. Опыт показывает, что при пользовании этими машинами в глине может остаться около половины (а иногда и более) камней. В дальнейшем эти камни будут в значительном своем количестве перемолоты гладкими вальцами или бегунами, что, однако, вызывает быстрый износ бандажей и частые ремонты. Бегуны мокрого помола используют при наличии в глинах трудноразмокаемых включений и для обработки плотных глин и глин, содержащих известковые включения. Предварительное (грубое) дробление непластичных твердых материалов в керамической технологии производят в щековых или конусных дробилках, работающих по принципу раздавливающего и разламывающего действия. Степень измельчения в щековой дробилке 3-10, а в конусной – 6-15. Среднее и мелкое дробление, грубый помол непластичных материалов выполняется с помощью бегунов, молотковых дробилок, валковых мельниц. Молотковая дробилка обеспечивает высокую степень измельчения (10-15), однако влажность дробимого материала не должна быть более 15 %.
После измельчения фельзит и глина, а так же отдозированные со склада сырьевым материалов зола, жидкое стекло и ЛСТ поступают в глиномешалку. Подача и дозировка сырья на большинстве кирпичных заводов происходит при помощи ящичных питателей. В глиномешалке происходит смешивание всех сырьевых компонентов, а так же увлажнение. Увлажнения происходит путём добавления влаги и равномерного распределения среди керамической массы, которая образовалась в результате смешивания сырьевых материалов.
В настоящее время на многих керамических и кирпичных заводах широко применяется увлажнение глины паром. Этот способ состоит в том, что в массу подается острый пар, который при соприкосновении с холодной глиной конденсируется на ее поверхности. В результате пароувлажнения обрабатываемая масса нагревается до 45-60 оС. Пароувлажнение имеет существенные преимущества, так как улучшается способность массы к формованию, что обуславливает уменьшение брака при формовке и повышение производительности ленточных прессов на 10-12 %, снижение расхода электроэнергии на 15-20 %. В результате пароувлажнения улучшаются сушильные свойства массы, что позволяет сократить продолжительность сушки сырца на 40-50 %.
После этого керамическая масса поступает на бегуны мокрого помола, производительность которых зависит от свойств обрабатываемой глины, её влажности, от размера катков, их массы, и числа оборотов, формы чаши бегунов, расположения скребков. На кирпичных заводах применяют бегуны мокрого помола с вращающимися катками неподвижной частью.
Иногда производят дополнительную обработку керамической массы, которая осуществляется в вальцах тонкого помола, дырчатых вальцах или в глинорастирателе.
Для формования кирпича по пластическому способу на кирпичных заводах применяют вакуум- пресс с фильтр-смесителем. В случае если керамическая масса имеет недостаточную влажность для пластического формования, в вакуум- прессе перед формированием керамического бруса происходит увлажнение смеси, путем разбрызгивание капель воды. Форма изготавливаемого изделия и его поперечные размеры определяются формой и размерами выходного отверстия вакуум- пресса.
Выходящий из пресса глиняный брус режут на отдельные части при помощи полуавтоматических и автоматических резательных станков.
Большинство современных кирпичных заводов оборудовано устройствами для искусственной сушки кирпича-сырца, которые по режиму работы подразделяются на сушилки периодического (камерные) и непрерывного (туннельные) действия.
Сушка кирпича-сырца необходима для увеличения механической прочности и подготовки к обжигу. В данной курсовой работе будет использоваться сушка непрерывного ( туннельная) действия.
Сушилки непрерывного действия (туннельные) являются наиболее современным сушильным агрегатом в кирпичной промышленности. В туннельной сушилке кирпич-сырец, находящийся в вагонетках, в течение цикла сушки перемещается через весь туннель от одного его конца к другому. Регулировать режим сушки кирпича-сырца можно изменяя количество подаваемого теплоносителя и его температуру. Скоростной режим сушки обеспечивается при подачи больших объёмов теплоносителя, имеющего высокую температуру, что позволяет увеличивать скорость продвижения вагонеток в туннеле. При увеличении объёма в теплоносителе, подаваемого в единицу времени, уменьшается или полностью расслаивание теплоносителя при его прохождении в туннеле. Срок сушки кирпича-сырца, изготовленного из пароувлажнёной массы сокращается примерно на 30 %. При скоростном режиме сушки кирпича-сырца температура теплоносителя на входе в туннель составляет 90-120 °С, а на выходе из туннеля- 30..40 °С. Относительная влажность теплоносителя на выходе из туннеля достигает 85…90 %. Скорость теплоносителя в туннеле должна быть около 3 м/с. Разрежение на выходе теплоносителя из туннеля составляет 0,108…0,204 мм. рт.ст. Продолжительность сушки кирпича-сырца 12…20 часов. Расход тепла на сушку кирпича-сырца в туннельных сушилках ниже , чем в камерных. Существенным преимуществом туннельных сушилок перед камерными является то, что туннельные могут быть оснащены аппаратурой, обеспечивающей автоматическое регулирование процесса сушки. Продолжительность процесса сушки и качество высушенного кирпича-сырца в значительной степени зависят от плотности и системы садки сырца на сушильных вагонетках. Необходимо обеспечить равномерность омывания теплоносителем сырца и получение надлежащей температуры и относительной влажности теплоносителя в различных частях сушилки. Недостаток туннельных сушилок в том, что в них наблюдается расслоение теплоносителя и более интенсивная сушка сырца на верхних полках. Устранение расслоения и равномерная сушка сырца по высоте туннеля достигаются перемешиванием теплоносителя в туннеле путем устройства воздушных завес за счет дополнительной подачи воздуха сверху в отдельных местах туннеля струйками с большой скоростью .
Завершающей стадией технологии всех изделий строительной керамики является их обжиг. При обжиге изделия окончательно формируется структура материала, т.е. происходит спекание керамики, в результате чего сырец из конгломерата слабосвязанных частиц превращается в достаточно твердое тело.
Строительные материалы и изделия обжигают в промышленных печах. Промышленной печью называют установку технологического назначения, в которой посредством теплового воздействия при относительно высоких температурах изменяется агрегатное состояние обрабатываемого материала, его химический состав либо его кристаллическая структура.
Многорядовые (по высоте) туннельные печи, применительно к обжигу стеновой керамики, обладают крупным недостатком – большим перепадом температур по высоте, достигающим в зоне подогрева 420 0С, который на участке максимальных температур уменьшается до 20-40 0С. борьба с этим перепадом осуществляется главным образом путем рециркуляционных потоков газов («завес»), нагнетаемых вентиляторами как в зоне подогрева, так и в зоне охлаждения на нескольких позициях по длине печного канала. Борьба эта не всегда успешна.
Второй недостаток – трудности настройки аэродинамического режима
Лучшие условия эксплуатации туннельных печей достигается при наличии давления или разряжения в зоне обжига порядка 0,0013-0,0041 мм рт.ст. и не выше 0,0136 мм мм.рт.ст. во избежание выбивания горячих газов и «горения» и быстрого износа вагонеток.
Совершенствование конструкций туннельных печей с целью увеличения обжигаемой физической массы изделий (увеличение теплоемкости), совершенствование горелок для развития длины факела, а также полноты сжигания жидкого топлива, улучшение теплоизоляции пода – все это приводит к определенным успехам, но не исключает необходимости разработки и совершенствования конструкций печей для однорядного скоростного обжига.
В конструктивном отношении современные туннельные печи обладают некоторыми особенностями. Конструкция свода плоская, что упрощает постройку печи, позволяет расширить печной канал и обеспечить работу автомата – укладчика. Толщина кладки стен туннельных печей снижена до 0,5м., благодаря применению огнеупорных блоков 30-40% пористости, наружная поверхность стен покрыта дюралюминием с хорошей отражательной способностью. Поверх свода помещена теплоизоляция в виде вспученного вермикулита. Кладку пода (на вагонетках) осуществляют из крупных огнеупорных фасонных блоков, изготовленных из пористого (30-40%) корундомуллитового кордиеритового или дистенового огнеупора, обеспечивающего огнеупорность, теплоизоляцию и постоянство объема.
Наблюдается тенденция увеличения ширины туннельной печи, что возможно при переходе на более совершенный способ сжигания топлива с получение длинного факела горения и равномерным развитием температурного поля.
Обжиг кирпича производят в печах периодического и непрерывного действия. В кирпичной промышленности из печей периодического действия применяют преимущественно камерные печи. Из печей непрерывного действия применяют главным образом кольцевые и туннельные.
Периодические печи используют для обжига кирпича на заводах малой мощности. Загрузка и разгрузка этих печей производится при сравнительно высоких температурах, что обуславливает тяжелые условия труда обслуживающего персонала. Камерные печи или горны отличаются значительной трудоемкостью обслуживания, большой неравномерностью температур по высоте печи.
Для обжига кирпича широко применяют кольцевые печи, которые, несмотря на то, что они изобретены в 1858г., широко используются и в настоящее время. Они отличаются высокой тепловой экономичностью, возможностью использования низкосортных видов топлива, перехода с одного вида топлива на другое без каких-либо значительных переделок, высокой удельной и общей производительностью.
Весьма существенным недостатком кольцевых печей является то, что в рабочей зоне садки и выгрузки (выставки) кирпича очень высокая температура: например, в рабочей зоне выгрузки температура в летние месяцы достигает 80 0С и более. При этом садка и выгрузка кирпича производится вручную. На новых и реконструируемых кирпичных заводах строительство кольцевых печей не производится.
Туннельные печи имеют значительные преимущества перед печами периодического действия и кольцевыми печами. Садка кирпича-сырца на вагонетки туннельных печей и выгрузка обоженного кирпича с этих вагонеток производится вне печи, в нормальных температурных условиях, что значительно облегчает труд обслуживающего персонала и дает возможность механизировать трудоемкие процессы садки и выгрузки кирпича.
Процесс обжига можно условно разделить на 4 периода( зоны):
1) Досушка, которая производится при температуре до 150 °С, в процессе чего происходит удаление химически связанной влаги. В данной зоне образуется значительное количество водяного пара. Этот период является одним из наиболее опасным, так как при интенсивном выделении водяного пара изделия могут трескаться и разрываться. Поэтому досушка должна происходить при незначительных температурных перепадах, не более 30°С по толщине изделия.
2) Подогрев, который осуществляется в интервале 150…800 °С. В данной зоне происходят химические процессы: удаляется химически связанная вода; выгорают органические добавки при температуре 500…600 °С ( или органические примеси). При нагревании 600…800 °С происходит разложение карбонатных включений в образованием углекислого газа. В процессе выгорания органических примесей начинается процесс усадки( уменьшения изделий в объёме). При температуре 700…800 °С происходит дегидратация каолинита, с образованием метакаолинита. После нагревания больше 800 °С( 850…860 °С) происходит образование силлиманита.
3) Зона обжига происходит при температуре 800… 1200 °С. При этом образуется свободные оксиды алюминия и кремния , которые соединяются в дальнейшем в безводный алюмосиликат- муллит.
4) Охлаждение кирпича в печи до температуры 500 °С. Величина температурного периода по толщине изделий должна быть не более 20…30°С. Это исключает появление внутренних напряжений в изделий и их растрескивание. После 500°С охлаждение изделий может происходить значительно быстрее, со скоростью снижения 120…130 °С/ час.
После обжига вагонетка направляется на разгрузку и пакетеровку. Упаковка проводится автоматом-пакетеровщиком термоусадочной пленкой. Вывоз пакетов готового кирпича осуществляется электрокаром, загрузка пакетов на транспорт осуществляется козловым краном.
- Главная -
- Чертежи -
- Промышленность -
- Промышленность строительных материалов -
- Технологическая схема производства золокерамических кирпичей
Технологическая схема производства золокерамических кирпичей
0
278
6444
34
0
20
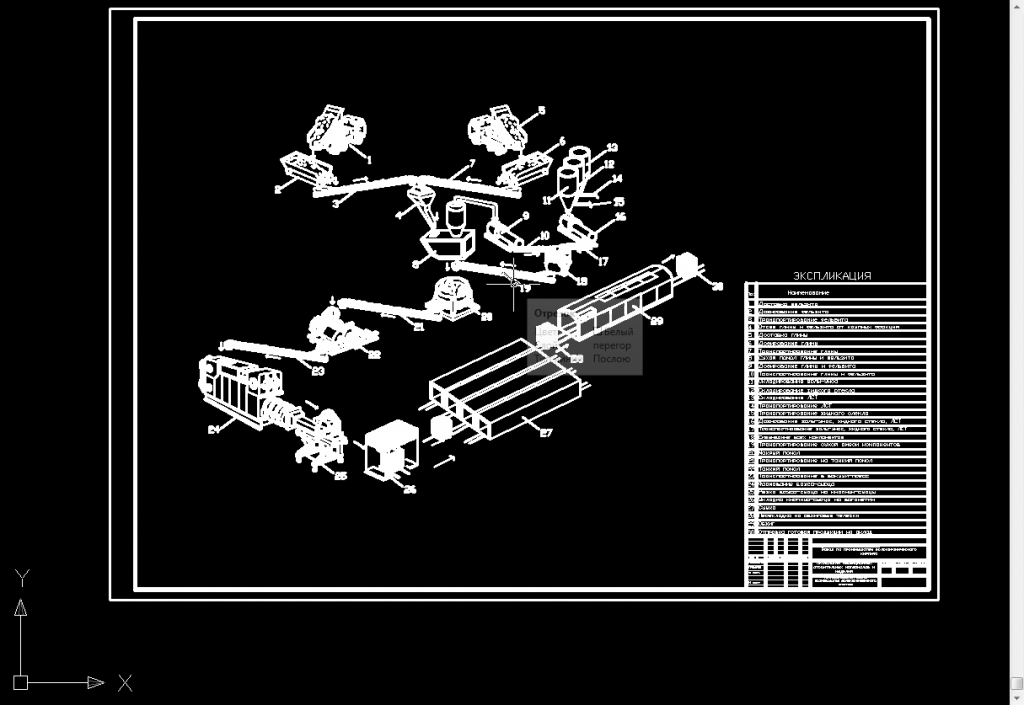
Сообщить о проблеме
Автор
Дата
24.05.2012
Язык
Русский
Состав
Технологическая схема
Софт
AutoCAD, DWG
Как открыть?
Отзывов пока нет
Содержимое архива
Чтобы скачать чертеж, 3D модель или проект, Вы должны зарегистрироваться
и принять участие в жизни сайта. Посмотрите, как тут скачивать
файлы
Отзывов пока нет
Чтобы задать вопрос, необходимо войти
Войти с помощью:
Ссылка на логин через google
Ссылка на логин через vk
Ссылка на логин через yandex