Описание технологического процесса
НАК - основной компонент полимера. МА - добавляется в качестве второго компонента для улучшения окрашиваемости волокна и его эластичности. SAMPS - добавляется в качестве третьего компонента для обеспечения окрашиваемости волокна катионными красителями за счет введения в полимерные цепочки группы ~SO3Nа. SAMPS является гидрофильным соединением, благодаря чему его присутствие в полимере снижает скорость десольватации на стадии формования и улучшает потребительские свойства. ДМФ - растворитель мономеров и образующегося из них полимера. Азодиизобутиронитрил (АЗДН), выпускаемый под названием «порофор ЧХЗ-57», инициатор реакции полимеризации - при температуре реакции разлагается на свободные радикалы, которые инициируют процесс полимеризации. Яблочная кислота используется для связывания катионов железа в реакционной смеси (так как они ухудшают цвет прядильного раствора и волокна - вызывают пожелтение) и поддерживает рН реакционной среды в пределах 6,5-7,5.
Фильтрация прядильного раствора
С целью очистки прядильного раствора от различных механических примесей проводится его фильтрация с помощью фильтров непрерывного действия(ФНД).
С целью предотвращения образования взрывоопасных смесей в приемном и буферном баках прядильного раствора они находятся под азотной подушкой.
Основной поток фильтрованного прядильного раствора разделяется на три части и подготавливается к формованию на идентичных технологических линиях, обеспечивающих работу соответствующих прядильных линий.
Для улучшения фильтрации прядильного раствора его температура должна поддерживаться 52-56 °С подачей горячей воды в змеевик, вмонтированный в рамы фильтр-пресса.
Основной поток фильтрованного прядильного раствора разделяется на три части и подготавливается к формованию на идентичных технологических линиях, обеспечивающих работу соответствующих прядильных линий.
Нагревание прядильного раствора
Прядильный раствор нагревается с 40-50 С до 52-56 С с целью снижения динамической вязкости примерно с 6,7 до 4,5 Пас, что необходимо для проведения формования волокна в оптимальных условиях.
Нагревание ведется в теплообменниках пластинчатого типа, в качестве теплоносителя используется конденсат с температурой 70-90 С. Применение теплоносителя с более высокой температурой может привести к местным перегревам и пожелтению прядильного раствора.
Введение паст добавок и растворенных отходов волокна
Пасты добавок и растворенные отходы волокна вводятся в прядильный раствор перед статическими смесителями лабиринтного типа. При получении волокна, окрашенного в массе, в смеситель 1-ой технологической линии подается паста пигментов. Двуокись титана вводится в прядильный раствор для получения матового, без блеска волокна.
Эффект матирования достигается при содержании в волокне 0,3-0,5 % двуокиси титана. Паста двуокиси титана готовится с концентрацией около 21 %.
Для исключения потерь мокрых неокрашенных отходов волокна, образующихся при работе прядильных линий, они растворяются в ДМФ, и полученный раствор полимера вводится в прядильный раствор.
Отходы волокна, окрашенного в геле реализуются потребителю.
При введении пасты пигмента в прядильный раствор получается окрашенное в массе волокно. Недостаток этого способа крашения по сравнению с крашением волокна в геле - получение нестандартных по цвету (переходных) партий волокна при переходе с цвета на цвет. Для уменьшения выпуска волокна нестандартного цвета ассортимент на выпуск окрашенного в массе волокна составляется на длительный период, предусматривая выпуск волокна каждого цвета в значительных объемах и последовательный переход от самого светлого цвета к самому темному.
Суммарное содержание в готовом волокне пигментов в зависимости от цвета может составлять от 0,1 до 5 %. Пасты пигментов готовятся с концентрацией 1,5-23 % так, чтобы дозировка их в прядильный раствор составляла от 65 до 600 кг/час.
Прядение и отделка волокна
Получение волокна включает следующие основные технологические операции: формование, предварительную вытяжку, промывку, окончательную вытяжку, замасливание, сушку, нанесение антистатика, гофрировку.
Получение окрашенного в геле волокна включает дополнительные операции: нанесение красителя на волокно, термофиксацию красителя в волокне и промывку. Крашение волокна осуществляется между окончательной вытяжкой и первым замасливанием на 1-ой и 2-ой прядильных линиях.
Получение оптически отбеленного волокна включает операцию нанесения отбеливателя на волокно, при этом используется оборудование для нанесения красителя на волокно 1-ой или 2-ой прядильной линии. Волокно, окрашенное в массе, получается на 1-ой прядильной линии.
Вспомогательные технологические операции: циркуляция растворов ДМФ, очистка воздуха от паров ДМФ, обработка фильер и фильерных комплектов, приготовление растворов замасливателя и антистатика, приготовление красильных растворов.
Формование волокна
В процессе используется способ формования волокна из раствора полимера в органической прядильной ванне - водном растворе ДМФ.
Формование волокна осуществляется на двухстороннем прядильном агрегате поз. АП каждая сторона которого состоит из 4-х прядильных машин. Прядильная машина имеет 2 коагуляционные ванны из нержавеющей стали. В каждой каогуляционной ванне имеются 3 прядильных места, каждое из которых включает дозирующий шестеренчатый насос из специальной стали с производительностью 50 см3/об и 2 фильтрпальца из нержавеющей стали.
Прядильный агрегат имеет 48 прядильных мест. Жгут комплектуется из 8-ми прядей, всего нарабатывается 6 жгутов, по 3 жгута на каждой стороне агрегата.
Количество отверстий в фильере - 4781, диаметр отверстия 50 мкм, количество фильер в фильерном блоке – 16.
Прядильный раствор, подготовленный к формованию, прядильным насосом дозируется через фильтрпалец и отверстия фильер в осадительную ванну - раствор с концентрацией ДМФ 55-56 % и температурой 10-13 С.
Отработанный раствор прядильной ванны с концентрацией ДМФ примерно 58-60 % и температурой примерно 15-17 С сливается в бак раствора отработанной ванны.
Транспортировка свежесформованного волокна осуществляется системой хромированных вальцев из углеродистой стали с приводом от электродвигателя постоянного тока мощностью 5,5 квт.
Предварительная вытяжка волокна
Вытяжка волокна проводится для улучшения его физико-механических показателей. При вытяжке происходит ориентация макромолекул полимера вдоль оси волокна, уменьшение диаметров и уплотнение структуры элементарных волокон, которая однако, остается «открытой».
В зависимости от назначения и линейной плотности волокна общая кратность вытяжки составляет примерно 5-6. Вытяжка волокна осуществляется в 2 стадии: предварительная (с кратностью примерно 3) и окончательная (с кратностью примерно 1,7-2,0).
Предварительная вытяжка осуществляется на двухсторонней машине поз. МПВ. Вытяжка проводится между группами из 7-ми хромированных вальцев из углеродистой стали с покрытием из нержавеющей стали.
На каждой стороне машины осуществляется вытяжка трех жгутов. Вытяжка ведется в растворе с концентрацией ДМФ примерно 20-21 %. Температура раствора выдерживается в пределах 95-97 С
Для уменьшения содержания ДМФ в вытянутых жгутах проводится удаление из них части жидкости с помощью 2-х пар отжимных вальцев,каждая из которых состоит из стального и гуммированного вальцев.Необходимая степень отжима жидкости из волокна регулируется изменением давления воздуха в пневмоцилиндрах гуммированных вальцев.
Промывка волокна
Промывка осуществляется в двухсторонней машине поз. МП, каждая сторона которой имеет 15 ванн из нержавеющей стали, расположенных в 3 яруса (по 5 ванн в каждом ярусе).
Каждая ванна имеет хромированные вальцы из углеродистой стали с покрытием из нержавеющей стали для погружения жгутов в рабочий раствор и пару отжимных роликов на выходе из ванн для увеличения эффективности промывки.
Промывка волокна ведется раствором ДМФ с концентрацией примерно 0,2-0,4 % и температурой в 15-ой ванне примерно 55-70 С.
Окончательная вытяжка волокна
Окончательная вытяжка волокна осуществляется на двухсторонней машине поз. МОВ по конструкции аналогичной машине предварительной вытяжки поз. МПВ с той разницей, что группы вальцев каждой стороны машины имеют индивидуальные приводы от электродвигателей постоянного тока той же мощности. Вытяжка жгутов ведется в обессоленной воде, с температурой 95-97 С.
2.1.9 Замасливание волокна
Для повышения мягкости, эластичности волокна, улучшения текстильной переработки оно обрабатывается замасливателем. Операция осуществляется погружением жгутов в раствор замасливателя в обессоленной воде.
Первый замасливатель при обработке волокна не только распределяется на поверхности, но и проникает внутрь волокна, находящегося в виде микропористого геля. В качестве первого замасливателя используются продукты отечественного производства. Нанесение замасливателей ведется при температуре 35-45 С.
Крашение волокна
Оборудование для нанесения красителя на волокно включает красильную машину поз. МК.
Каждая сторона машины имеет ванну из нержавеющей стали, 2 беличьих колеса для погружения жгута в красильный раствор, опорный валец между колесами и отжимные вальцы, расположенные на выходе жгута из ванны. Беличьи колеса и валец выполнены из углеродистой стали и хромированы
Температура раствора в ванне выдерживается в пределах 20-60 С воды. На выходе из отжимных вальцев установлены микропереключатели, с помощью которых при отсутствии жгута автоматически закрывается регулирующий клапан подачи красильного раствора в ванну и срабатывает световая сигнализация. При остановке отжимных вальцев подача красильного раствора также прекращается. Для быстрого перехода на выпуск неокрашенного волокна предусмотрен подъем беличьих колес двумя пневмоцилиндрами.
Термофиксация красителя в волокне
Перед термофиксацией проводится уменьшение ширины жгутов с 375-425 мм примерно до 250-300 мм на жгутосужающем устройстве ЖСУ. На обеих линиях имеется по 3 двухсторонних устройства, на каждой стороне которых обрабатывается по одному жгуту. Устройство представляет собой систему вогнутых хромированных вальцев, смонтированных на станине из углеродистой стали.
Термофиксация красителя в волокне осуществляется в двухсторонней машине МФК на каждой стороне которой обрабатывается по 3 жгута.
Каждая сторона машины состоит из 3-х пар камер (подвижных верхних и стационарных нижних) из нержавеющей стали, которые через трубчатые распределители подается острый пар низкого давления. Для предупреждения конденсации пара камеры обогреваются паровыми змеевиками из нержавеющей стали, конденсат из них отводится с помощью конденсатоотводчиков. Пар к камерам и змеевикам подается по гибким шлангам с оплеткой из нержавеющей стали.
Транспортировка жгутов через машину термофиксации осуществляется питающим станом ПС и тянущим станом ТС установленными соответственно до и после машины.
Промывка волокна от красителя
После термофиксации осуществляется промывка волокна от избытка красителя на машине МПВК расположенной после тянущего стана ТС.
Секция промывки состоит из ванны из нержавеющей стали и 2-х пар отжимных вальцев, расположенных на выходе жгутов из каждой ванны. Обессоленная вода подается на жгуты через специальное сопло на выходе их из второй ванны. Каждая ванна имеет хромированный валец из углеродистой стали для погружения жгутов в воду. Температура воды выдерживается в пределах 35-55 C.
После промывной машины МПВК волокно поступает на двухсторонний жгутонаправитель ЖН1, предназначенный для подготовки к обработке на одностороннем оборудовании.
Затем волокно поступает на жгуторасправитель ЖР, представляющий собой хромированный валец, смонтированный на станине из углеродистой стали.
Сушка волокна
Сушка волокна ведется в сушилке СВ. Она состоит из 24 индивидуальных секций сушки, каждая из которых включает барабан, вентилятор и калорифер. Барабаны изготовлены из листов нержавеющей стали с перфорированной поверхностью. В каждой секции осуществляется непрерывная циркуляция горячего воздуха вентилятором из барабана через калорифер и волокно снаружи барабана.
Жгуты в сушилке проходят последовательно в нижней части нечетных барабанов и в верхней части четных барабанов, прижимаясь к их поверхности потоком воздуха. Температура воздуха в сушилке выдерживается в пределах от 140 до 160 С и обеспечивает снижение влагосодержания в волокне примерно от 55 до 0,5-2 %.
Нанесение антистатика на волокно
В качестве антистатика используются продукт импортного производства – синтезин.
Нанесение антистатика осуществляется на машине МНА после сушилки СВ и производится поверхностным способом. Антистатик наносится при температуре окружающей среды.
Машина для нанесения антистатика представляет собой систему вальцев и систему подачи антистатика. Антистатик наносится на жгут с двух сторон при помощи двух металлических вальцев, вращающихся навстречу жгуту и погруженных в ванночки с раствором антистатика. Содержание антистатика на волокне регулируется изменением скорости вращения вальцев, погруженных в антистатический раствор, в пределах 7-18 об/мин.
Гофрировка волокна
Гофрировка индивидуальных жгутов осуществляется на машине МГ.
Перед гофрировкой волокно переводится в термопластичное состояние обработкой острым паром низкого давления. Затем жгут вальцами подается в специальную камеру сминания, где он, упираясь в имеющееся там волокно, получает извитость. При необходимости острый пар низкого давления может подаваться и непосредственно в камеру сминания. В зависимости от назначения производимого волокна величину его извитости можно регулировать изменением сопротивления выходу жгута из камеры сминания. После придания волокну извитости оно обрабатывается воздухом с температурой 115-125 С для удаления влаги, внесенной при гофрировке.
Гофрировка индивидуальных жгутов осуществляется на машине МГ.
Накопление волокна
Гофрированный и высушенный жгут укладывается на транспортер гофрированного жгута ТГЖ по 6 жгутов на каждый и направляется в накопительный бункер БН, представляющий собой полусферическую металлическую емкость вместимостью около 300 кг волокна. Бункер разделен вертикальными секторами на 6 отсеков для каждого из жгутов. Из накопительного бункера, в зависимости от назначения, жгут может поступать к резательным машинам или жгутоукладчикам.
Укладка жгута
Укладка каждого жгута осуществляется на индивидуальных жгутоукладчиках ЖУ1-3, оснащенных устройствами подачи пустых и наполненных жгутом контейнеров.
Через распределяющее и направляющее устройство ЖН2 жгут постоянно отбирается вращающимися металлическими и прижимными гуммированными вальцами жгутоукладчика. Затем жгут с помощью лотка, совершающего колебательные движения, укладывается в подвижный металлический контейнер по всей площади. По мере наполнения контейнера жгут в нем подпрессовывается пневматически управляемой плитой пресса. Прессование заканчивается автоматическим отключением счетчика метров жгута или кнопочным отключением.
После заполнения контейнер перемещается на подвижную роликовую выходную площадку позиция, а затем на борт самоходной тележки.
Укладка и подпрессовка жгута выполняется в автоматическом, при необходимости в полуавтоматическом режиме.
Резка жгута
Жгутовое волокно режется на резательных машинах РМ1-2 с натяжным устройством НЖ. Жгут подается в резательную машину из накопительного бункера БН через распределительное устройство с вогнутыми роликами, которое соединяет два жгута вместе. Роль тянущего механизма выполняют вращающиеся металлический и прижимной гуммированный валики натяжного устройства. Автоматическая синхронизация скоростей тянущих вальцев и ротора резательной машины со скоростью оборудования прядильно-отделочного агрегата обеспечивает равномерность натяжения жгута.
Упаковка жгута и нарезанного волокна
Упаковка жгута в кипы осуществляется на однокамерном гидравлическом прессе. Принцип упаковки следующий: Контейнер со жгутом подается в зону пресса. Открываются полуднища контейнера и жгут опускается в прессующую камеру, расположенную ниже верхней отметки пола. Кипа образуется за счет гидравлического сжатия с последующей обвязкой уплотненного жгута проволокой.
Подача и отбор контейнера, а также вывод кипы механизированные с ручным, автоматическим или комбинированным управлением.
Упаковка нарезанного волокна в кипы производится на гидравлическом 2-х камерном прессе карусельного типа. Принцип упаковки следующий: через загрузочное устройство нарезанное волокно подается в подпрессовочную камеру. Кипа образуется в прессовочной камере за счет гидравлического сжатия с последующей обвязкой проволокой уплотненного волокна. Подача нарезанного волокна непрерывная. Вывод кипы механизированный с ручным или полуавтоматическим управлением.
- Главная -
- Чертежи -
- Промышленность -
- Технологическая схема производства волокна Нитрон-д
Технологическая схема производства волокна Нитрон-д
0
289
11319
6
0
40
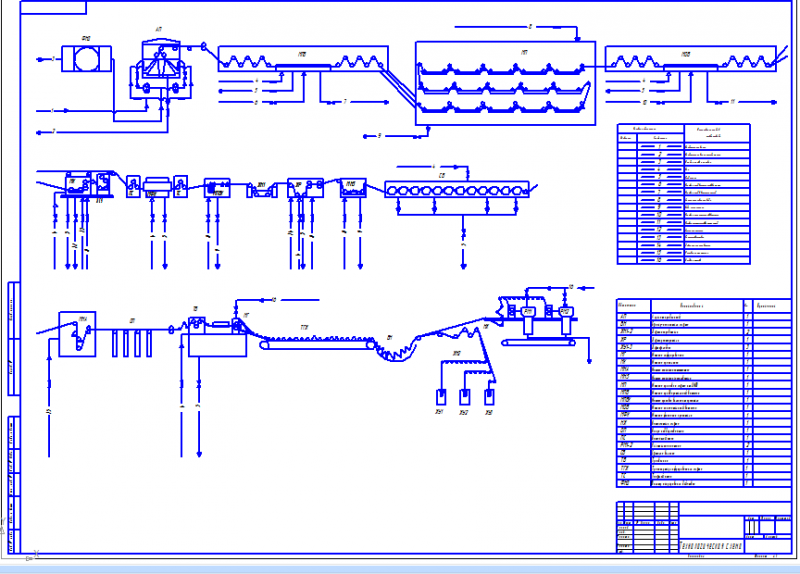
Сообщить о проблеме
Автор
Дата
09.12.2011
Язык
Русский
Состав
технологическая схема, спецификация
Софт
Компас v12, CDW
Отзывов пока нет
Содержимое архива
Чтобы скачать чертеж, 3D модель или проект, Вы должны зарегистрироваться
и принять участие в жизни сайта. Посмотрите, как тут скачивать
файлы
Отзывов пока нет
Чтобы задать вопрос, необходимо войти
Войти с помощью:
Ссылка на логин через google
Ссылка на логин через vk
Ссылка на логин через yandex